Family dairy farmers the Kidds from Quernmore near Lancaster have spent the last 10 years future-proofing their milking enterprise in the hope of building a sustainable farming business for the next generation.
Building a Sustainable Farming Business
Booth Hall Farm is home to 150 all year-round calving Holsteins plus followers. Due to limited local expansion options, the family has focused on shrewd investments to save labour and improve animal welfare to allow the farm to run as efficiently as possible. The herd now produces 9,000 litres per cow per year from 360 grass acres plus some ground earmarked for growing whole-crop cereals.
Brothers David and Neil Kidd will be the fourth generation to run the enterprise and now farm in partnership with their mother Maureen and father Edwin, who still live in the farmhouse. Neil does most of the milking, with David focusing on feeding and rearing the calves. Ultimately, Edwin and Maureen will step back from the day-to-day running of the farm to allow their sons to take on more responsibility and drive the business forward.
Investing in Calf Housing
“Our first major investment was a new parlour, which was followed by improved cubicle housing for the cows,” David Kidd says. “But our latest project is a new re-located, totally bespoke calf rearing building, which is already transforming the way we rear our herd replacements. Going forward, investment will be channelled into projects like this that save us time. We do not really see ourselves getting much bigger, so it’s all about efficiency.”
David says the old calf accommodation wasn’t ideal, although the calves were reared individually and did do quite well. “However, we were spending too much time washing down the pens and bucket feeding. I was spending about 45 minutes a day making up feeds and feeding calves. We wanted a much easier system.”
In consultation with their parents, David and Neil decided to re-configure the calf housing on the home site. The old calf shed was demolished and this released ground ideally located for a new house for Neil. Following extensive research, the Kidds then erected a brand new, bespoke calf building, giving them the opportunity to build from scratch what they now see as fit-for-purpose, easily-managed accommodation for calves.
“The relocation of the calf house will ultimately allow Neil to move back onto the farm with his family and mean he can be around for any night calvings. It also means we can now rear our dairy youngstock as efficiently as possible,” David says.
Installing a Computerised Calf Feeder
The Kidds also sought advice from local Volac representative Jason Short about computerised calf rearing systems and following his input they became the first unit in the UK to install the new Urban Alma Pro computerised feeder.
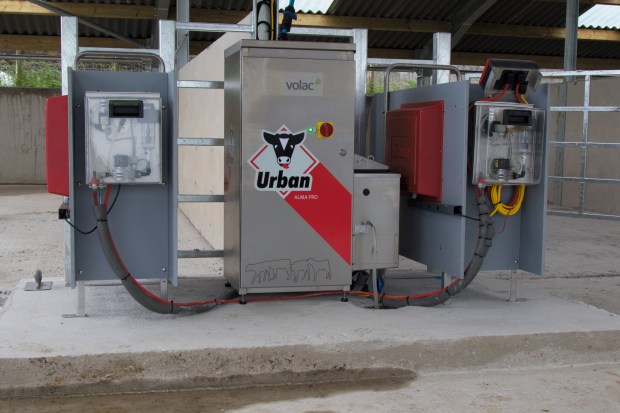
“Automatic milk feeding machine technology has really moved on and this innovative new computerised system really ticks all the boxes for us,” David says.
Volac’s Jason Short points out that the new machine is a great step forward at a time when the industry is focusing on sustainable, high performance calf rearing.
“The system is capable of feeding up to 120 calves individually and accurately during the pre-weaning milk feeding period. It also allows parallel feeding, which typically means no waiting time at the drinking station and up to four calves can be fed simultaneously. But what is really innovative in this new feeder is its improved hygiene system, which incorporates automatic teat cleaning with disinfection after every calf feed. And, uniquely, the ability to deliver the right dose of any necessary medications, such as electrolytes, to the right calf, at the right time,” he says.
The machine recognises an individual calf’s ear tag when it enters the feeding station and allocates the correct milk portion and concentration accordingly. Once the calf has taken its feed the teat will re-track and be sprayed with cold water and a disinfectant solution. Machine hygiene status has also been enhanced to allow sanitisation with acid and alkali up to four times a day, which cleans and sterilises the feed lines and bowl.
David appreciates these potential hygiene and medication benefits, but is particularly impressed with the touch-screen control system and the fact that it can connect seamlessly via WiFi to his phone or tablet.
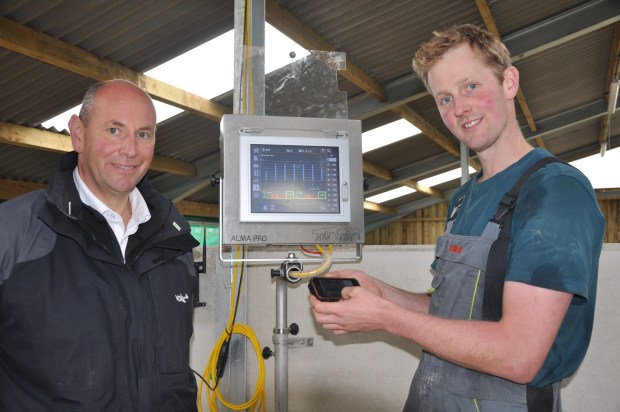
“The calf feeding curves are easily programmable and thanks to an in-line temperature sensor it always mixes and feeds milk at a consistent temperature. The machine automatically knows the daily feeding requirements of each and every calf, so every animal gets exactly what it needs. You can also easily see how often an animal drank and how much it consumed – and if it doesn’t drink enough the machine triggers an alarm on your smart phone to alert us to a potential issue, even if you are not on the farm,” he says.
David says initially he was a bit nervous about group housing the calves, but the new building design means the rearing environment is good and the machine takes care of optimum nutrition. Early life colostrum feeding protocols are also excellent, which means the calves always enter the new rearing building in the best possible shape.
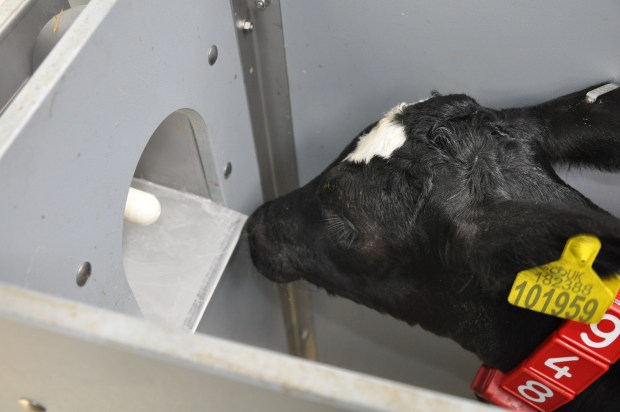
“We separate all our calves from the cow at birth and tube feed them to make sure they get what they need, aiming to get four litres of high quality colostrum into them via two x two litre feeds within the first six hours of life. Our vet also blood tests calves periodically to check the effectiveness of our colostrum feeding.”
Efficient Youngstock Rearing
The Kidds believe the new calf house and computerised milk feeder have transformed the efficiency of their youngstock rearing.
“It’s certainly released a lot of my time to focus in other jobs,” David says. “But we’re also rearing high quality milking herd replacements at optimum efficiency, which calve down between 22 and 26 months of age.”
“The first calves went into the new building at the end of June 2017 and all we have to do is train the calf onto the teat and the rest is done automatically. About 10% of all the work done on a dairy farm is dedicated to the calves and a big part of that is mixing and feeding milk, as well as cleaning out any buckets and/or hutches or pens. We still have to clean out, but the group pen design and extra space and capacity we built into the original building plan means this is now as straightforward as possible. It’s made a huge difference to the time we spend on this part of our dairy farming operation.”
If you would like to find out more about the Urban Alma Pro, get in touch today.
Published on: 16 November 2017
View all articles